ATI Metals Year Two
Summer 2019
About ATI
Allegheny Technologies produces high performance materials and also flat rolled products. They create titanium and nickel alloys for industries ranging from aerospace to kitchen appliances. The Pittsburgh based company has $4 billion in sales and has a valuation of about $3 billion as of 2019. I interned at the Washington PA facility where they rolled and finished plates, a surprisingly lucrative business.
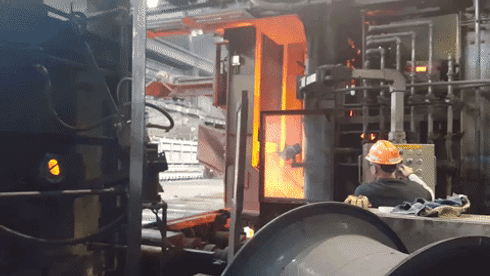

Summer 2019, ATI
Maintenance Engineering Internship
In my second year at ATI, my boss gave me the opportunity to see a different side of things and sent me to maintenance. This time, I arrived with more confidence and know how. I worked more with a team of engineers on more daily issues this time around. Rather than analyzing data all day, I would learn how the mill really functioned and how employees and management interacted.
My Work
As a maintenance intern, my work was more fast paced, daily activities. Unfortunately, working on a project for two days and moving on does not yield impressive looking presentation. However, this was the most fruitful internship because of the nature of the work. Here is a summary of my larger responsibilities:
CAD Prints
Drawing, Dimensioning, Labeling
Daily Checks
Examining, Reporting, Analyzing
Outage Project
Managing, Supervising, Inspecting
Macro and Micro Learning
Absorbing, Seeking, Applying

CAD Projects
CAD drawings are needed for manufacturing. The prints I created will be brought to life and utilized in the future to better ATI.
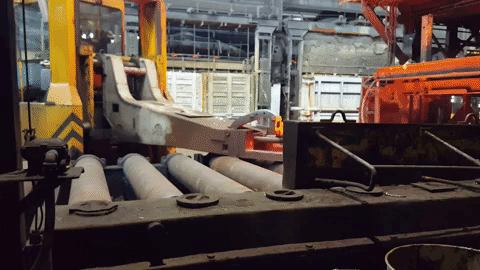
My Process
Measurements
The first step in creating drawings is to get the correct dimensions. Since I was making sketches of objects that already existed, I had to measure every single part including details like welds.


Drawing
Then, I used AutoCad 2012 to create the drawing. I had some modeling experience so this was not the hardest part.
Bill of Materials
I created the bill of materials so ATI could easily order everything we needed. Finding the standardized way to write parts was new to me.

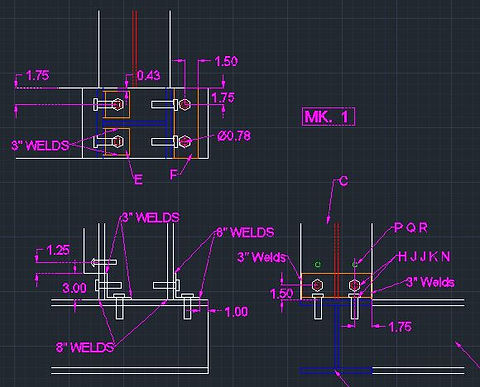
Dimensions
I annotated by following previous formats. I also asked machine shop workers how I could improve them since I had to create with other people's perspective in mind.
Review
I knew I could create the shapes on CAD, but I did not know the proper way to show it. From close ups, tomarks, to bolt sizes, to material lists, I needed the professional touch. I frequently made changes to small details to accommodate the industry standards.
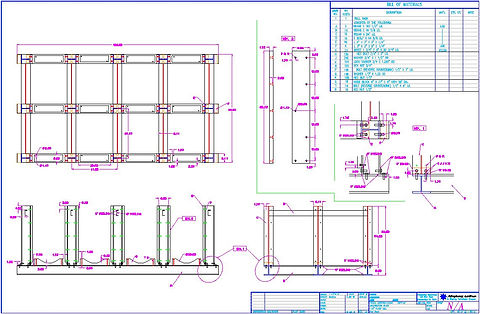
Learned
AutoCAD 2D, 3D
How to Professionalize Drawings
Proper Dimensions and Welds
Accurate Tolerances
Material Recognition
Creating a Standard Bill of Materials

Daily Inspections and Reporting

Irregularities
Safety hazards include leaking pipes, safety hazards, and anything out of the ordinary. I had daily inspections for anything that could cause trouble.
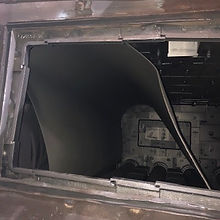
Blast Inspection
Blasting is a necessary finishing process that throws shot at the plates. Unfortunately, this machine eats itself up from the inside. Weekly check ups were required.
.jpg)
Reporting
With just a handful of maintenance managers, I added an extra pair of eyes and ears to relate progress and issues to those in charge. This means I had to learn and know about each job.
Learned
Mill Functionality
Attention to Detail
Focus on Safety
Fight Complacency Through Questioning
Problem Recognition
Outage Project
Wheelabrator Bag Houses
During the plant shutdown, I had the responsibility to supervise an outside contractor repair a filter system. Luckily for me, they kept it interesting.
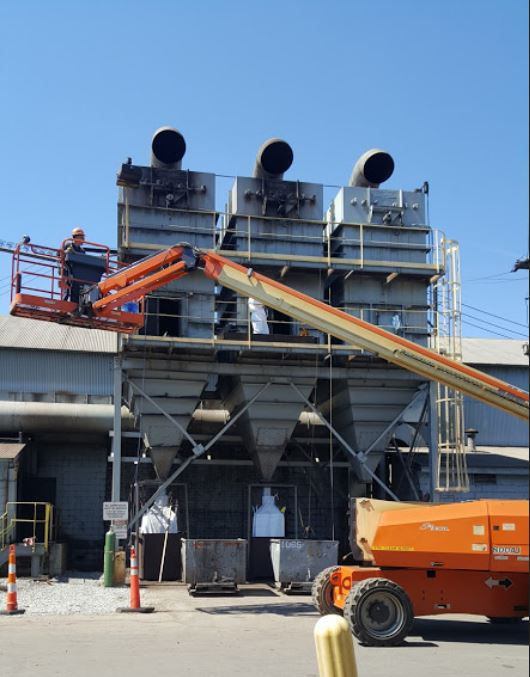


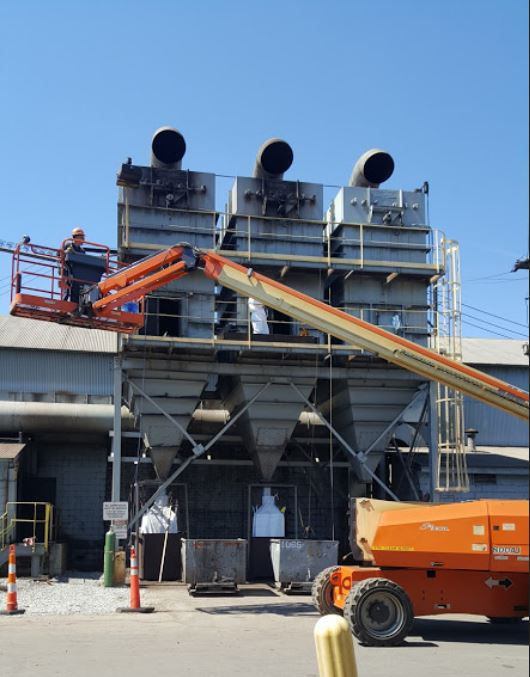
Primary Tasks:
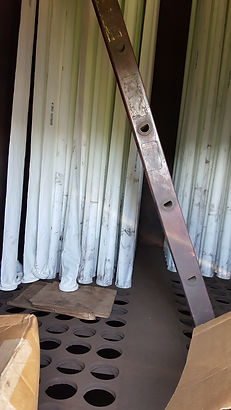

Replace Filter Bags
Repair Shakers
Personal Duties

Collaborated with the Foreman

Managed Logistics

Assisted in Decision Making

Inspection
Results
After a rough three days, the bags and vibration system was repaired and running smoothly, ready for another few years.

Learned
How to Handle Contractors
Balancing Stern and Helpful Tones
How Logistic Problems Are Solved
Fire Prevention
Contractors Vary in Skill
Outside Work Must Be Inspected
Supplies Should Be Checked Up Front
Baghouse Mechanics
Work Projects Fall Behind Just Like Personal Projects
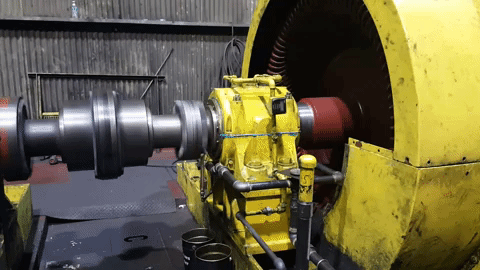
First Hand Learning
This task was not exactly tangible. The work involved every interaction with a coworker and every minute of free time. There is so much to soak in at ATI, which cannot be done on a computer. I had to learn how to seek out initiative and ask questions on my own.

Meetings
Varying in size, I participated in daily safety and production meetings, and even led a few.
First Hand
I learned from engaging with floor employees and my own observation.
Relationships
I learned how to handle working with the same people every day to dealing with salesmen.
Tours
Through ATI, I have toured four other facilities, each with a different purpose and environment.
Online Reading
I have looked into bearings, motors, cranes, annealing processes, DC current, filter systems, etc.
Business
From financials to vendors, I had the opportunity to experience how business is carried out.
Taking Inniative
With a fast paced work environment, its is easy for an intern to get swept away and forgotten while everyone does their own job. I had to take initiative and use the knowledge and relationships I had to better the company. Work often has to be pursued and pushed pushed for, especially if different parties are involved.  Sometimes I would learn from an engineer or a floor employee or occasionally take on a task independently.

New Employee Maps
There is plenty of difficulty with helping as an intern. Everyone knows more than you. However, one aspect I had down pretty good was being a new employee. I used my two years of experience to creates map and material flow chart of the operations at Washington. This knowledge should cut down on the steep learning curve of starting and help with location jargon.
I have given these materials to a new rotational engineer and presented it during a tour of the facility. My work will now be given to new hires and potentially other tours to provide answers to the fundamental questions that it took me two summers to comprehend.
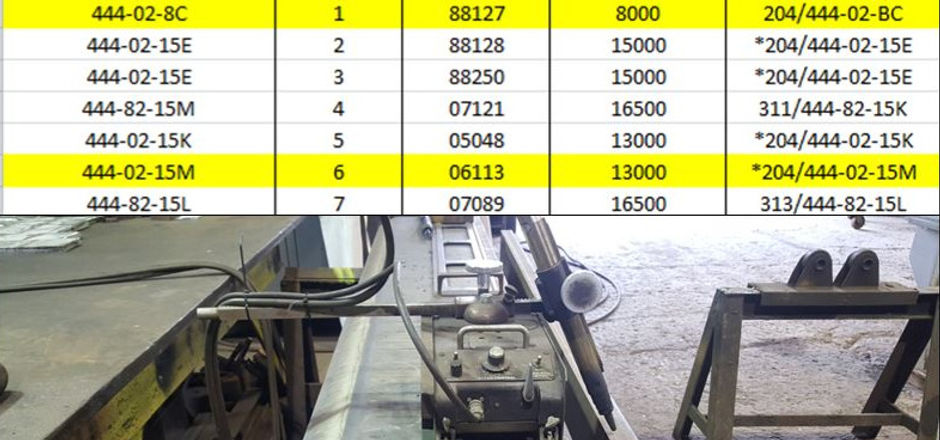
Assisting Odd Jobs
Being present and visible combined with the environment of maintenance, led me to do small jobs that are not quite noteworthy. I have updated locations of steel grabs for inspections, brought parts to different workers, and assisted with solutions. This type of work was daily, but I had to seek it out.