Puzzle Box
For my ME design course, we had a semester long project consisting of idea evaluations, prototypes, and presentations. I was assigned to a group of 4 for 12 weeks of my junior year.
Opportunity
We start with the project needs and overview necessary for my group.
Idea Generation
We moved to brainstorming and systematic processes to come up with the best ideas.
Concept Selection
We then analyzed ideas and weighed them by our criteria.
Prototyping
The group made 3 prototypes with varying features and modifications.
Final Results
This is the final report, product, and outcome after 12 weeks.


About the Project
My ME340 class was largely project base with some labs, quizzes, and lectures that helped you with the project. The assignment prompt can be found below.
​
Essentially, my group was to manufacture a product to fill an opportunity. The product was already decided as a puzzle box, but left all other decision making to us.
​
They placed us into groups within a few weeks and we started on our proposal. Since this was a class, I have fantastic documentation of all the work my group put in.

Opportunity
We did not begin with brainstorming; rather, we began with a macro-view of our task. We had to understand the opportunity, specifications, audience, and goal of the project.
We decided on creating a puzzle box for a Penn State STEM escape room to be used by students. In the presentation slides below, we explain puzzle boxes, how they can implemented in escape rooms, and possible mechanisms in puzzle boxes.
Concept Selection
In the same links as above, here is our concept selection process.
While it is easy to pick a few good options and hope, decision making should be more in depth. In this section, we narrowed down our choices and then let the math take over to achieve the true optimal result.

Concept Screening
This method narrows down our wide spectrum of ideas by simply tallying if it is good or bad in a category.

Creating an AHP Matrix
The Analytical Hierarchy Process matrix is a tool that gives a weight for each need. The AHP is critical for our most important tool- Concept Scoring.

Concept Scoring
This method was the deciding factor in our mechanism choosing. By combining the importance of each need with the best concepts, we could make our final decisions.
Prototyping
We made 3 prototypes before arriving on our final product. Each one tested different looks and features. Designing a puzzle box and actually building one are two very different tasks.
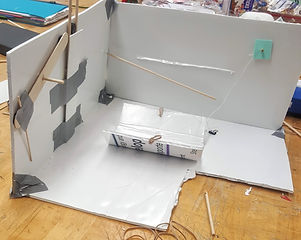
Alpha 0
To experiment with basic concepts, we used cheap art supplies. By doing this exercise, we were forced to create mechanisms and look at how the whole box would function together. Even though it was not pretty, this was a vital exercise in getting started. The alpha 0 was built while we were still debating concepts and ideas.

Alpha 1
Now that we had some experience and had ideas we wanted to incorporate, we created our alpha 1 prototype. Because we were on a college budget, the materials were cheaper and easily modifiable. This box gave us an idea on overall size, fasteners, materials, and mechanism performance.
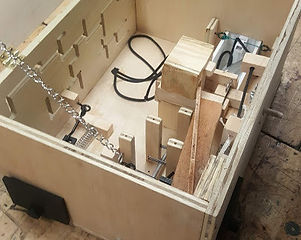
Alpha 2
This prototype was serious. Most of the materials are reused for the final design, so this box closely resembles our final beta. It was fully functional and used mechanisms we improved from the last designs. It also contained 3D printed drawers and a machined part.
How to Solve
![]() Step 1 | ![]() Step 2 | ![]() Step 3 |
---|---|---|
![]() Step 4 | ![]() Opening |
Learned
Managing Deadlines
Teamwork With Different Views
Leadership
Brainstorming Methods
Customer Needs
Screening and Scoring Matrices
Prototyping
Formal Reports
Presenting in a Team
Simple Machines/ Mechanisms
Designing for Use
Laser Cutting
Building vs Designing
Working with Teammates with Differing Priorities